The process of structural changes in the global automotive industry is being pushed forward by the rapid development of the electric vehicle industry. The face of high technical barriers to breaking, but it occupies 50% to 70% of the electric vehicle powertrain manufacturing costs of vehicle batteries (especially lithium-ion batteries), some automakers began to struggle: how to choose the battery technology?
To clarify the context of this issue, let us first take a look at the measures adopted by the top car giants in the global market at the current stage:
Since 2006, Volkswagen has formed an alliance with Japan's Sanyo to jointly develop a new generation of nickel-hydrogen battery systems. After that, the two parties jointly developed HEV's new generation of large-capacity lithium battery system in 2008 and plans to officially put it into the market in 2012.
In early 2009, Ford announced that it had signed a five-year supply contract with Johnson Controls-Saft, which will supply on-board battery systems to its plug-in hybrid models. In December of the same year, the two parties signed a lithium-ion battery supply contract for the Transit pure electric vehicle.
South Korea's Hyundai International stated at the beginning of November 2009 that it is expected that LG Chem Ltd. will jointly establish a lithium battery plant before 2013 and will provide on-board battery systems directly to Hyundai and Kia after production. Just three months before the modern announcement of this will, U.S. General Motors has selected LG Chem as its battery supplier for its hybrid SUV model. According to reports, SB LiMotive Ltd., a battery joint venture between Germany's Bosch and South Korea’s Samsung SDI, may also reach a supply agreement for lithium batteries with GM this year.
In Japan, Nissan, NEC, and NEC Dongjin had established a joint venture in 2007 to jointly produce lithium-ion batteries. In order to fully meet Nissan's future demand and supply to other vehicle manufacturers, NEC Tokin plans to expand its lithium-ion battery electrode capacity by 50 times by the end of this year.
While cooperating with third-party independent battery manufacturers, auto giants including General Motors, Renault-Nissan, etc. are also building direct-controlled battery production plants. Among them, GM has officially announced that the lithium battery factory in Michigan is the first battery plant controlled by the US automaker. The Renault-Nissan Alliance's lithium battery plant in Sunderland, UK, has also started construction. It is expected that volume production will be realized by early 2012. The lithium battery produced by this plant will be directly supplied to Renault and Nissan's electric vehicles.
However, compared to the model of joint cooperation with battery manufacturers, the case of self-production of batteries by automakers has not yet dominated the current stage. Therefore, by analyzing the battery technology acquisition methods of the above-mentioned representative vehicle manufacturers in Europe, the United States, Japan, and Korea, we can basically reach the following conclusion: That is, joint independent third-party manufacturers with strong R&D and production capabilities. The development of vehicle-mounted battery systems is a universal strategy adopted by major automobile manufacturers worldwide at this stage.
In response, some consulting agencies and industry analysts also agreed that it is an inevitable trend that vehicle manufacturers and individual battery manufacturers jointly develop battery systems. "Strong cooperation will, on the one hand, strengthen the capital strength of battery development and ensure the funds needed for industrialization. On the other hand, it will accelerate the integration of the vehicle and battery interface and will accelerate its industrialization."
However, we must realize that the current status of this so-called “strong and strong joint development†is based on the premise that electric vehicles have not yet been industrialized. Once the relevant core technical problems have achieved breakthroughs and the electric vehicles are mass-produced within a predictable five or ten years, will the automakers be willing to give big profits to the battery manufacturers? As the “chain owner†of the industry chain, will automakers wait for opportunities to seek other means including independent research and development of battery systems to strictly control the outflow of profits?
According to Chinese local professional automotive information provider for the K-car last week has launched a topic survey (conducted 2010 September 13 to September 17) show that 1948 people in the industry to participate in the vote, 63 percent said, During the mature industrialization of electric vehicles, independent third-party battery manufacturers will remain the main owners of vehicle-mounted battery technology. Due to nearly 2,000 pollers participating in the survey, the number of parts and components companies from China's local vehicle manufacturers accounted for about 70%. Therefore, to a certain extent, the voting data reflected the Chinese auto industry’s The basic judgment of the problem.
We believe that with earlier investments and a complete R&D system, coupled with the advantages in talent pools, some independent battery manufacturers will hold market power in the battery field for a longer period of time in the future. Moreover, another variable we cannot ignore is that the strong independent battery makers have not met the current market performance that has been stalled. Out of optimistic expectations for the future electric vehicle market and the pursuit of profits in the automotive battery market, these battery companies are also continuously increasing R&D investment, expanding production bases, further consolidating market position and firmly holding possession of core technologies.
As the world leader in the automotive lithium-ion battery market, Japan’s Sanyo intends to occupy more than 40% of the global automotive lithium-ion battery market by 2015.
Bosch in Germany and Samsung SDI in South Korea to strengthen their future strength in the energy industry and jointly funded the establishment of a battery joint venture SB LiMotive Ltd., which has signed a 10-year cooperation agreement with Delphi in the United States and plans to start Delphi in 2012. Supply lithium-ion battery. In addition, Cobasys and BMW, both suppliers of nickel-hydrogen batteries for automotive use in the United States, are customers, and supply agreements with general-purpose lithium batteries are expected to be reached this year.
Japan's GS Yuasa denied that its lithium-ion battery plant is expected to begin construction in October this year in its local Shito City, Shiga Prefecture. It is understood that the company and Honda, Mitsubishi and other OEMs have built joint ventures to produce electric vehicle batteries. According to its interim report (2010-2012) announced last May, it will invest a total of 50 billion yen in lithium-ion battery business in the next three years.
Japan’s Toshiba, another major battery maker, is also increasing its investment in building factories. According to its plan, by 2015 it will strive to achieve sales of 200 billion yen and occupy more than 10% of the global market share of vehicle-mounted batteries.
The most recent expansion of the battery manufacturer comes from the United States A123 company, which recently opened a new plant covering an area of ​​291,000 square feet in Livonia, Michigan. The plant is expected to provide lithium batteries for 30,000 plug-in hybrids annually after full operation, and is expected to become the largest lithium battery production base in North America. At the same time, A123 is currently preparing for the supply of lithium batteries for BMW hybrids.
In addition to the above-mentioned independent battery manufacturers, similar supporting companies such as the German mainland and Magna of the United States have also devoted their efforts to lithium battery business.
After the strong capture of these two camps, the prospect of independent development of battery systems by automakers is not so optimistic. According to another set of data from Gasgoo.com's survey results, 60% of the nearly 2,000 voters opposed all vehicle manufacturers at the present stage have invested huge amounts of money in the battery field.
However, given the “chain owner†position of OEMs, whether in terms of financial strength or channel control, they have absolute advantages, and then the trade-offs between comprehensive costs and profits, we believe that at the current stage, joint research and development Under the model, in the future, some more ambitious OEMs will launch strategic acquisitions of independent battery manufacturers, most likely in the future after the fully competitive electric vehicle market.
For the electric vehicle industry, which the Chinese government is trying hard to develop, does the local vehicle manufacturer follow the model of other vehicles in the world? Gasgoo.com's survey of local auto industry professionals in China shows that 42% and 34% of voters believe that “joint R&D†and “acquisition of third-party battery manufacturers†are more feasible for automakers to master battery technology. s method.
According to the analysis of access to battery technology for some of China's local mainstream OEMs, the above arguments are confirmed by facts.
In December 2009, as the largest domestic automaker SAIC and the United States A123 Company announced the establishment of Shanghai Jiexin Battery System Co., Ltd. with a ratio of 51:49, the two parties will jointly develop, manufacture and sell onboard battery systems.
In the middle of this year, BAIC Group, another large domestic state-owned holding company, finalized a cooperation framework with South Korea's electric vehicle manufacturers CT&T and SK Energy, and the three parties jointly invested to form a joint venture in China. Among them, BAIC and CT&T are responsible for the production of electric vehicles and SK is mainly responsible for the supply of lithium batteries.
In addition, Changan, Dongfeng, and Chery and other OEMs in China’s “four large and four small†factories also cooperate with domestic and foreign independent third-party battery manufacturers in terms of vehicle batteries, thereby realizing the final “assembly†of electric vehicles. Foreign battery manufacturers have also used this supply contract to gradually infiltrate the supply system of Chinese domestic OEMs.
As one of the most significant market specimens, the investment boom in China's auto industry has already benefited significantly from the automotive battery market. At the same time, the industrial bubble is faintly visible. According to our understanding, the large and small lithium battery manufacturers in China's domestic market have already reached nearly 1,000, and few actually have mastered the development of core components. As for whether China's automakers will invest in R&D for lithium batteries in the context of lower operating profit in the traditional business model and unclear development of electric vehicle industrialization, we expect caution.
We believe that the acquisition of on-board battery technology by most local OEMs in China will not take independent research and development for quite some time. Joint and M&A of third-party battery makers will remain the lowest cost and effective strategy. . At the same time, with the continuous involvement of foreign battery companies, China's lithium battery market in the future a highly competitive knockout will also be inevitable.
The relevant survey data is as follows:
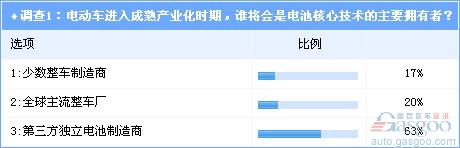
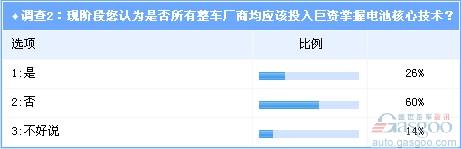
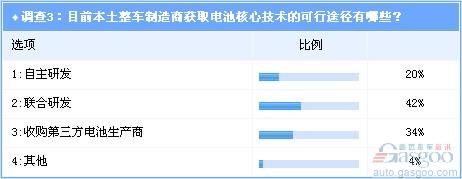
Waste Tire Pyrolysis Plant,Continuous Waste Tyre Pyrolysis Plant,Pyrolysis Plant,Environmental Waste Tire Pyrolysis Plant